A Comprehensive Guide to Starting a Quality Control Program in Your Business

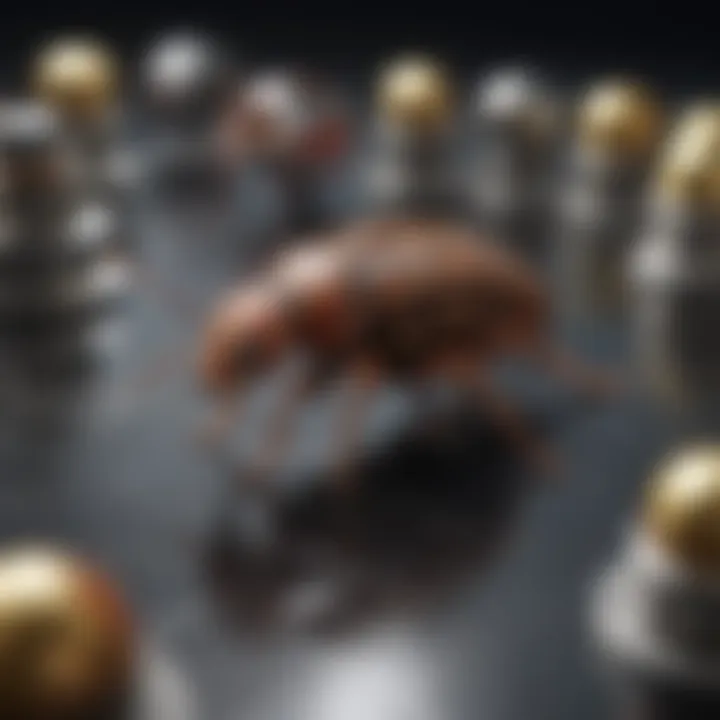
Preventive Pest Control Strategies
When it comes to implementing a robust pest control program, starting with preventive measures is crucial. A proactive approach can save both time and money in the long run. One of the key areas to focus on is protecting the house exterior. This involves inspecting and sealing any cracks or openings that pests could use to enter your home. Additionally, clearing debris around the house and maintaining a clean outdoor environment are effective ways to deter pests from taking up residence on your property.
Yard maintenance plays a significant role in preventing pest infestations. Establishing essential yard care routines, such as regular mowing, trimming, and clearing away fallen leaves, can help create a less hospitable environment for pests. Implementing methods like using pest-resistant plants and keeping shrubs pruned can further contribute to a pest-free yard.
Ensuring indoor cleanliness is another vital aspect of pest control. By employing expert cleaning tips and techniques, you can eliminate sources of food and shelter for pests within your home. Regular vacuuming, dusting, and decluttering can go a long way in maintaining a pest-resistant indoor environment.
Proper garbage disposal is often overlooked but critical in pest prevention. Using efficient waste disposal methods, like sealing trash bags and regularly emptying bins, is essential for keeping pests at bay. Understanding the importance of correct garbage disposal can significantly reduce the likelihood of attracting pests to your property.
In addition to these methods, exploring innovative pest prevention strategies can provide added protection for your home. Implementing measures such as installing mesh screens on windows and vents, using natural pest repellents, and incorporating smart landscaping practices can collectively fortify your defenses against unwanted intruders.
Introduction
It is essential for any business to establish a robust quality control program to ensure the consistent delivery of high-quality products and services. Quality control plays a pivotal role in enhancing customer satisfaction and optimizing operational efficiency. By adhering to stringent quality standards, businesses can safeguard their reputation in the market and foster long-term success. Understanding the core principles and objectives of quality control is paramount for laying a strong foundation for sustainable growth and competitiveness.
Understanding Quality Control
Definition of Quality Control
Quality control is the systematic process of maintaining standards and ensuring that products meet predefined criteria of quality and performance. By implementing quality control measures, businesses can identify and rectify defects in products, ultimately enhancing overall operational excellence. The meticulous examination of processes and products underlines the significance of quality control in fostering continuous improvement and customer loyalty.
Importance of Quality Control
Quality control is indispensable as it instills trust among consumers regarding the reliability and consistency of a company's offerings. By prioritizing quality control, businesses can mitigate risks associated with product failures, thereby safeguarding brand reputation and market position. Embracing quality control practices not only leads to operational efficiency but also sets the stage for sustainable growth and enhanced competitiveness.
Setting Quality Control Objectives
Identifying Key Objectives
Identifying key objectives is crucial in delineating the specific outcomes that a quality control program aims to achieve. By defining clear objectives, businesses can align their efforts towards streamlining processes, reducing errors, and enhancing overall product quality. These objectives serve as guiding principles for employees, empowering them to contribute effectively towards achieving organizational excellence.
Aligning Objectives with Business Goals
Aligning quality control objectives with broader business goals is essential for driving synergy and cohesion within the organization. By ensuring that quality control objectives are aligned with overarching business objectives, companies can maximize the value derived from their quality initiatives. This alignment fosters a unified approach towards quality management, culminating in enhanced operational outcomes and sustainable business growth.
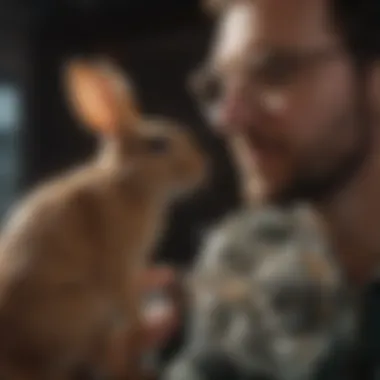
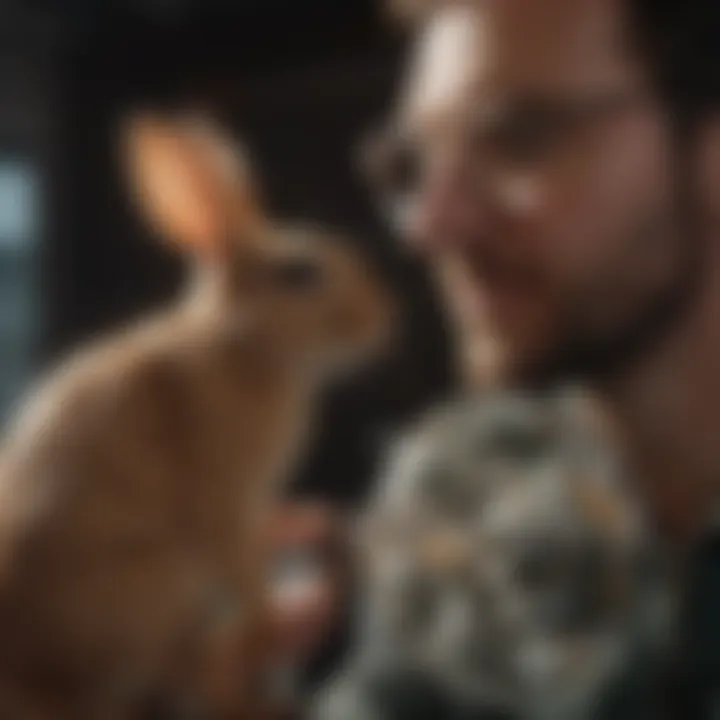
Key Benefits of Implementing Quality Control
Enhanced Product Quality
The foremost advantage of implementing quality control is the substantial improvement in product quality. By adhering to rigorous quality standards, businesses can elevate their offerings to meet or exceed customer expectations, thereby building a loyal customer base. Enhanced product quality translates into increased customer satisfaction and a stronger market presence, setting the stage for long-term success.
Improved Customer Satisfaction
Quality control directly impacts customer satisfaction by ensuring that products consistently meet specified quality benchmarks. Satisfied customers are more likely to become loyal advocates of a brand, driving repeat business and positive word-of-mouth referrals. By prioritizing customer satisfaction through quality control measures, businesses can forge lasting relationships with their client base, fostering trust and loyalty.
Reduced Costs and Wastage
One of the significant benefits of quality control is the reduction in costs associated with defects and wastage. By identifying and rectifying quality issues early in the production process, businesses can avoid costly recalls and rework, leading to substantial savings. Additionally, minimizing wastage through stringent quality control measures not only enhances cost-effectiveness but also underscores a company's commitment to sustainability and efficiency.
Planning Phase
In the realm of quality control programs, the planning phase plays a pivotal role in ensuring the successful implementation of effective quality control measures within a business. This crucial phase involves a meticulous evaluation of the current state of operations, identification of areas for enhancement, formulation of quality control policies, and allocation of necessary resources. By dedicating ample time and resources to the planning phase, businesses can set a strong foundation for a robust quality control program that aligns with their overarching goals and objectives.
Assessing Current State
Auditing Existing Processes
Auditing existing processes is a fundamental aspect of the planning phase in establishing a quality control program. This process involves a thorough examination and evaluation of the current practices and procedures within the organization. Identifying strengths and weaknesses in the existing processes allows businesses to pinpoint areas that require improvement or optimization. By conducting a comprehensive audit, companies can gain valuable insights into inefficiencies, bottlenecks, and potential risks, enabling them to implement targeted solutions effectively.
Identifying Areas for Improvement
Equally significant is the task of identifying areas for improvement during the planning phase. By scrutinizing existing processes and operations, businesses can uncover inefficiencies, redundancies, or lapses in quality control. Recognizing these areas for enhancement provides organizations with a roadmap for implementing strategic changes that can elevate product quality, streamline operations, and boost overall efficiency. Through a methodical approach to identifying areas for improvement, businesses can position themselves for long-term success and sustainability.
Formulating Quality Control Policies
Establishing Quality Standards
One critical component of the planning phase is the establishment of robust quality standards. Setting clear and measurable quality benchmarks ensures consistency and uniformity in product or service deliverables. Quality standards serve as guiding principles for employees, outlining expectations and requirements for maintaining high levels of quality throughout the production or service delivery process. By defining rigorous quality standards, businesses can instill a culture of quality excellence and continuous improvement within their operations.
Implementing Quality Assurance Measures
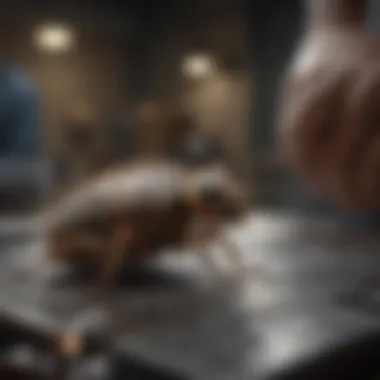
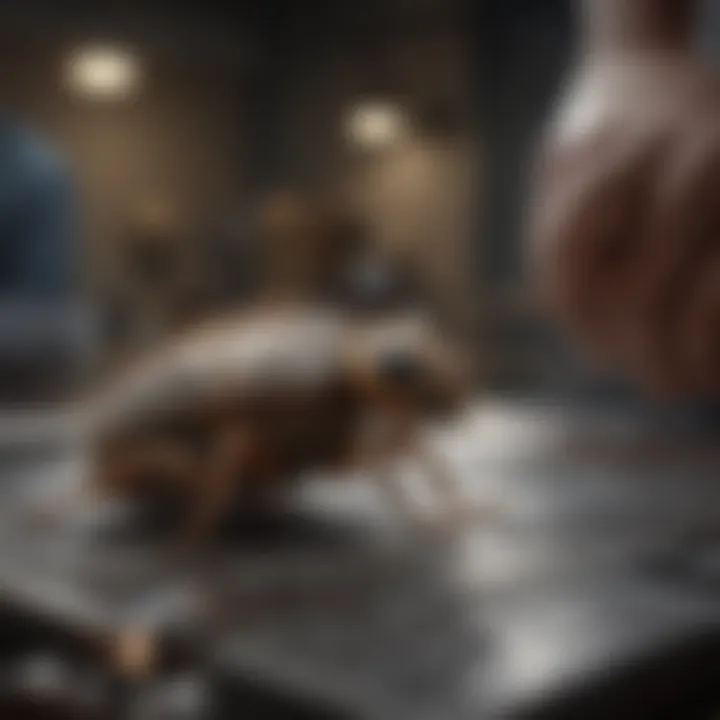
Complementing quality standards, implementing quality assurance measures is essential for upholding the established quality benchmarks. Quality assurance encompasses various processes and protocols designed to monitor, evaluate, and validate adherence to quality standards. By integrating quality assurance measures into the fabric of the organization, businesses can proactively identify and address quality deviations, ensuring that products or services consistently meet or exceed customer expectations.
Resource Allocation
Allocating Budget for Quality Control
Allocating a sufficient budget for quality control initiatives is a strategic investment that reinforces the importance of quality within the organization. Adequate financial resources enable businesses to implement cutting-edge quality control technologies, training programs, and quality monitoring systems. By earmarking resources specifically for quality control, companies demonstrate their commitment to delivering superior products or services and cultivating a reputation for excellence in the marketplace.
Training Staff on Quality Procedures
Equipping staff with the necessary knowledge and skills to uphold quality standards is a critical aspect of resource allocation in the planning phase. Training programs aimed at educating employees on quality procedures, best practices, and quality control protocols empower teams to execute their roles with precision and attention to detail. By investing in employee training, businesses nurture a quality-centric workforce capable of driving continuous improvement and maintaining consistently high-quality outputs.
Implementation Phase
In the intricate landscape of quality control programs, the Implementation Phase stands as a pivotal stage where theories and plans transform into actionable strategies. This phase, encompassing a strategic blend of Testing and Monitoring Procedures, is instrumental in elevating a business's quality standards to impeccable levels. By adhering meticulously to this phase, businesses can fortify their operations, enhance product quality, and secure heightened customer satisfaction.
Testing and Monitoring Procedures
Implementing Testing Protocols
Within the realm of quality control, Implementing Testing Protocols emerges as a critical facet that underpins the efficacy of the overall quality control framework. These protocols are meticulously crafted methodologies designed to scrutinize product quality, ensure adherence to standards, and pinpoint potential discrepancies. The key characteristic of Implementing Testing Protocols lies in its ability to provide a systematic approach to quality assessment, thereby fortifying the foundation of the quality control program. Moreover, the unique feature of Testing Protocols is their capacity to streamline processes, identify defects early on, and uphold product integrity. These aspects deem Implementing Testing Protocols a judicious choice for any business looking to refine its quality control practices.
Regular Monitoring and Evaluation
A cornerstone of the Implementation Phase, Regular Monitoring and Evaluation play a vital role in sustaining the efficacy of quality control measures over time. This component entails consistent surveillance of processes, continuous data collection, and diligent analysis to ensure seamless adherence to established quality standards. The key characteristic of Regular Monitoring and Evaluation is its proactive approach to quality oversight, enabling businesses to swiftly rectify deviations and uphold desired quality benchmarks. The unique feature of this phase is its capacity to instill a culture of continuous improvement, where real-time feedback and insights drive enhancements across the quality spectrum. Despite its advantages in bolstering quality control systems, challenges such as resource allocation and data interpretation may pose as potential drawbacks in the context of this article.
Addressing Non-Conformities
Root Cause Analysis
Addressing Non-Conformities necessitates a meticulous examination of root causes behind quality deviations, with Root Cause Analysis emerging as a fundamental investigative tool. This analytical process delves deep into production inefficiencies, operational lapses, or procedural discrepancies that lead to quality issues. The key characteristic of Root Cause Analysis lies in its ability to unearth underlying factors influencing product quality, thereby facilitating targeted interventions to rectify core issues. The distinct feature of this analysis is its emphasis on problem-solving at the source, ensuring sustained quality improvements. While advantageous in driving focused corrective actions, potential disadvantages may surface in instances where complexities in root cause identification impede swift resolutions.
Corrective and Preventive Actions
Complementing Root Cause Analysis, Corrective and Preventive Actions serve as the pragmatic response to quality deviations, emphasizing both short-term remediation and long-term prevention strategies. This phase focuses on mitigating identified issues promptly and devising preventive measures to avert similar occurrences in the future. The key characteristic of Corrective and Preventive Actions lies in its comprehensive approach to quality management, balancing immediate resolutions with forward-thinking strategies. Its unique feature lies in the strategic foresight applied, enabling businesses to preempt potential quality risks and enhance overall operational resilience. While undeniably advantageous in fortifying quality practices, challenges such as implementation complexities and resource constraints may pose as inhibitors to seamless execution.
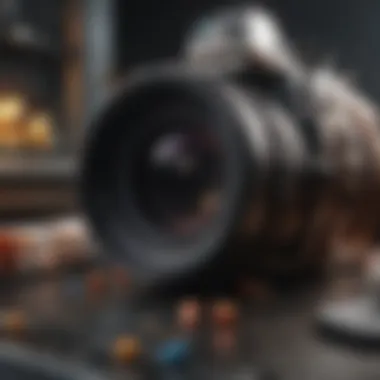
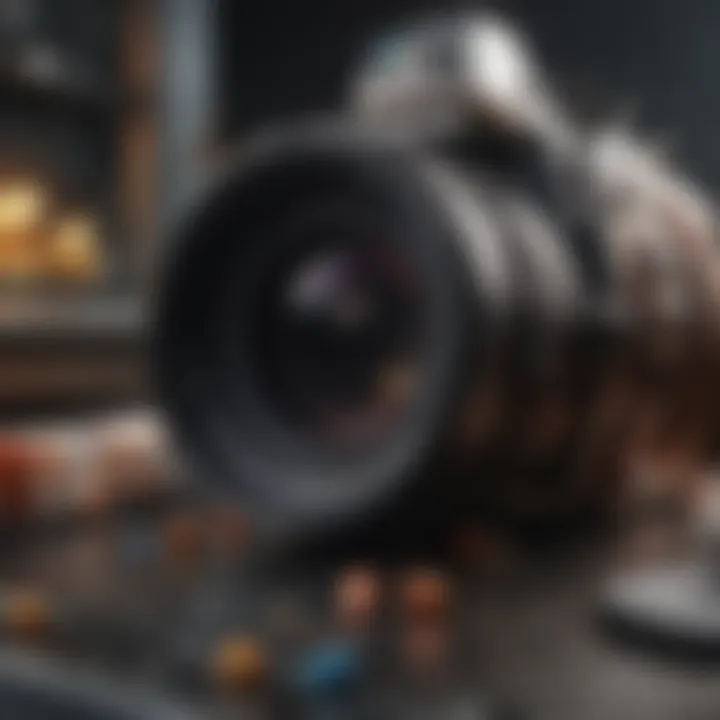
Continuous Improvement
Feedback Mechanisms
Crucial to the iterative nature of quality control programs, Feedback Mechanisms serve as the lifeblood that sustains perpetual enhancements and optimizations. These mechanisms entail gathering insights from customers, internal stakeholders, and operational data to steer meaningful quality refinements. The key characteristic of Feedback Mechanisms is their role in nurturing a culture of responsiveness and adaptability, where insights catalyze targeted quality improvements. Their unique feature lies in the intrinsic loop of information exchange, fostering an environment of ongoing learning and adaptation. While advantageous in driving customer-centric quality enhancements, challenges in feedback interpretation and implementation latency may underlie potential drawbacks in leveraging this aspect effectively.
Iterative Process Enhancements
Closing the loop on continuous improvement, Iterative Process Enhancements encapsulate the evolving nature of quality control paradigms, advocating for perpetually refined processes and standards. This facet underscores the importance of embracing change, embracing innovative solutions, and investing in ongoing process optimization. The key characteristic of Iterative Process Enhancements lies in their agile response to dynamic market demands and quality expectations, fostering a climate of innovation and advancement. Its unique feature is the intrinsic link between quality evolution and operational agility, empowering businesses to swiftly adapt to market fluctuations and customer preferences. While advantageous in promoting operational resilience, challenges such as resistance to change and organizational inertia may impede the seamless integration of iterative enhancements.
Evaluation and Review
In the realm of quality control programs, the Evaluation and Review phase holds profound significance as it serves as the compass guiding businesses towards sustainable success and growth. This section is pivotal in ensuring that the quality control processes remain aligned with the overarching business goals and objectives. By delving into detailed Performance Metrics, businesses can obtain a clear understanding of the efficacy of their quality control measures and make informed decisions for future enhancements and optimizations. Evaluation and Review allow businesses to gauge the effectiveness of their quality control systems, identify potential areas for improvement, and foster a culture of continuous advancement.
Performance Metrics
Establishing KPIs
Establishing Key Performance Indicators (KPIs) lies at the core of evaluating quality control effectiveness. KPIs are quantifiable metrics that help businesses assess their progress towards achieving specific objectives. By defining clear, measurable KPIs, organizations can effectively track their quality control performance and make data-driven decisions. The key characteristic of Establishing KPIs is its ability to provide actionable insights into the success of quality control initiatives. This strategic approach aids in ensuring that businesses remain on course towards meeting quality objectives and enhancing overall operational efficiency.
Measuring Quality Control Effectiveness
Measuring the effectiveness of quality control processes is essential for maintaining product quality and customer satisfaction levels. This aspect focuses on evaluating the impact of quality control measures on various facets of business operations. By analyzing key performance indicators related to quality control, businesses can pinpoint areas of strength and weakness, allowing for targeted improvements. The uniqueness of Measuring Quality Control Effectiveness lies in its ability to offer a quantitative assessment of the quality control program's success. This data-driven evaluation facilitates informed decision-making and continuous refinement of quality control strategies.
Feedback Analysis
Customer Feedback Analysis
Customer Feedback Analysis plays a crucial role in understanding consumer perspectives and refining quality control practices. By scrutinizing customer feedback, businesses can gain valuable insights into product performance, service quality, and overall satisfaction levels. The key characteristic of Customer Feedback Analysis is its capacity to bridge the gap between customer expectations and actual experiences. This analytical process enables organizations to address customer concerns promptly, enhance product offerings, and cultivate long-lasting relationships with clientele.
Internal Stakeholder Input
Incorporating Internal Stakeholder Input in the evaluation and review process enriches the quality control landscape by integrating diverse viewpoints and experiences. Internal stakeholders, including employees and management personnel, offer unique insights into operational dynamics and potential areas for improvement. The key characteristic of Internal Stakeholder Input is its ability to foster a collaborative environment where collective expertise contributes to the refinement of quality control strategies. This participatory approach enhances employee engagement, promotes transparency, and empowers stakeholders to actively contribute to quality enhancement initiatives.
Continuous Review
Regular Auditing
Regular Auditing is fundamental in maintaining the integrity of quality control processes and ensuring adherence to established standards. This practice involves systematic examinations of quality control procedures, documentation, and outcomes to verify compliance and effectiveness. The key characteristic of Regular Auditing is its role in identifying deviations from quality norms and facilitating corrective actions promptly. This process-driven approach enhances organizational efficiency, mitigates risks, and reinforces a culture of quality excellence.
Adjustments and Revisions
Implementing Adjustments and Revisions is essential for adapting quality control strategies to dynamic business environments and evolving market demands. This proactive approach to continuous improvement entails refining quality control protocols based on feedback, performance data, and emerging trends. The unique feature of Adjustments and Revisions is their ability to catalyze innovation, flexibility, and resilience within the quality control framework. By embracing adaptive strategies, businesses can optimize quality outcomes, drive operational agility, and stay abreast of industry changes and advancements.
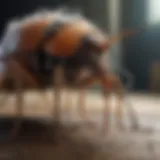
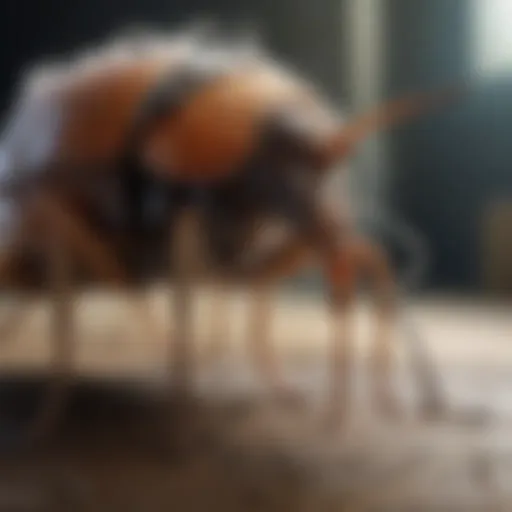